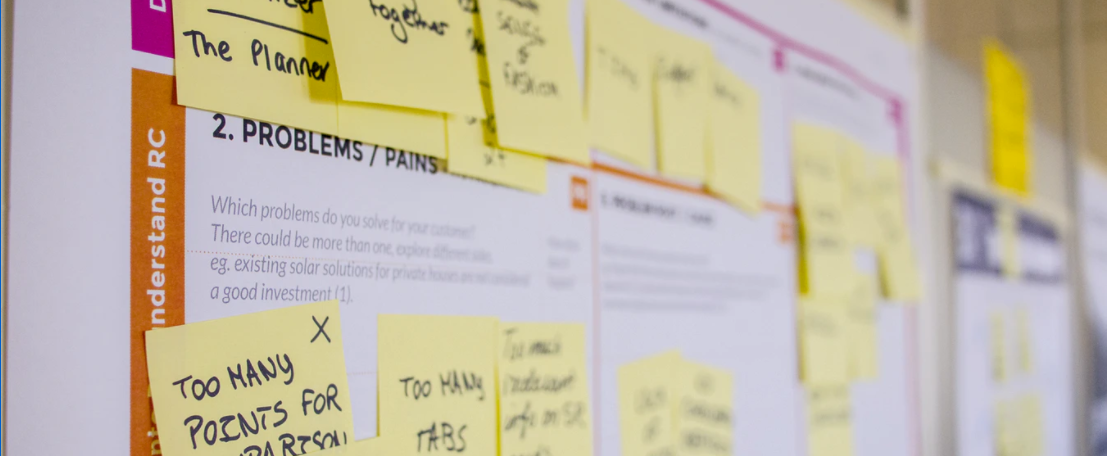
What are Standard Operating Procedures?
Standard operating procedures (SOPs) and work instructions are vital documents that lay out the who, what, when, and where for important procedures in your organization. SOPs are key to maintaining quality, protecting the public and employees, and meeting compliance and security regulation demands.Throughout this guide, we’ll help you understand how to write an SOP and when to use work instructions instead. Plus, we’ve included some strategies to make your SOP documents highly effective. Before we jump into the nitty gritty, let’s review some basics.What’s the difference between a work instruction and an SOP?
Work instructions and procedures each include step-by-step instructions to help users correctly perform a specific task. An SOP usually provides higher level information, while a work instruction takes the elements of a high-level process and adds more detail, specific assignments, and workflows to conform with company or industry standards.Why write an SOP instead of a work instruction?
A work instruction may be needed when your readers need to know the exact steps to achieve the desired outcome. A work instruction includes the most detail to perform a task and is typically used when the task is completed by one person from start to finish and includes fewer than 10 steps. An SOP, on the other hand, includes higher-level steps but not the detail of the work instruction. An SOP includes the macro-level steps to achieve the outcome and the who, when, and where.
For example, if we’re writing an SOP to make a peanut butter and jelly sandwich, the SOP might include five steps:
- Lay the bread on a plate.
- Scoop out the peanut butter and jelly.
- Spread the peanut butter and jelly on the bread.
A work instruction, on the other hand, would detail one or more of the steps; let’s use the second step as an example.
- Open the peanut butter by twisting the top to the right.
- Place the top of the peanut butter jar to the side.
- Take a butter knife and place the blade into the peanut butter.
- Move the knife from the right to the left to coat the knife.
- Extract the knife from the peanut butter jar.
You get the point. Work instructions are much more detailed than SOPs in most cases and should be used when users need that additional detail because the process requires a certain skill level or precise way of doing it, among other things.
[ Image ]
What are some common reasons to write an SOP?
Some common reasons to write an SOP:
- To meet compliance standards
- To maximize production requirements
- To ensure the procedure has no adverse impact
- To ensure safety
- To adhere to a schedule
- To prevent manufacturing failures
- For training
Check out our other blog about writing effective SOPs to learn more about best practices when writing your documents.
Learn how to write an SOP to create consistent outcomes in our SOP course!
Standard Operating Procedures Template
Standard Operating Procedures (SOP) are extremely valuable for people who produce release notes. When writing an SOP, consider:
- What information should be included (bug fixes, new features, known issues)
- What information shouldn’t be included (fixes or improvements that are not relevant to the task or not consumer-facing information)
- When information should be collected (how many weeks or days before release)
- Who collects the information (writer, product manager, testers)
- Which format to use for the output (HTML, PDF)
- How the review cycle works (when the document is sent for review, who reviews the document, how much time to review, how much time to implement edits)
- Who needs to approve the document (team leads, product owners, senior managers)
Now that you understand more about SOPs, let’s dive into work instructions.
What’s the difference between SOPs and work instructions?
While SOPs are top-level documents that tell employees which actions to take under a variety of circumstances, work instructions describe those actions in detail. These instructions aren’t necessarily long or verbose and should be clear and concise.When should you write work instructions instead of SOPs?
As mentioned, work instructions are ideal for situations that require details for specific actions. Some reasons to write work instructions instead of an SOP:
- When you need to outline specific steps to perform a specific task
- When you are outlining details for only one role
- When you need to provide mandatory guidance
- When you are focused on a single business unit
What are the best practices for work instructions?
Work instructions should be narrowed to an individual task within an SOP. Make sure that any terminology used is clearly defined or well-known by anyone who might use the instructions, considering that it may be used by someone whose first language isn’t English and/or is not literate. As in all good writing, consider the audience, including pre-existing knowledge and primary concerns in the situation.Writing work instructions can be as simple as bulleted lists or as complex as illustrated instruction flows. The overriding requirement is clear instructions for completing a given task. It's a good idea to include checklists in your instructions so employees can confirm that the directions or steps have been carried out correctly.
Even if you have fantastic SOPs, processes can break down if specific work instructions are missing or inadequate. After all, an employee might know that s/he needs to check a certain assembly, but if s/he doesn’t know which steps to take to perform that action, the employee might not know what to check for or how to complete the check.
How can you make the most of work instructions?
Writing work instructions is an activity that can be learned. Whether for use in a business environment or to meet specifications, work instructions, like all scientific or technical writing, follow a certain “writing recipe,” and it’s one that our professional instructors at Hurley Write specialize in teaching.What’s next for your SOPs and work instructions?
The best way to ensure your team is making the right decisions with your company’s SOPs and work instructions is to keep learning.Explore our many helpful courses:
Sign up today, and take your business to the next level.
Writing SOPs Exceptional Technical WritingProfessional Communication in Today’s Workplace
To learn more about Hurley Write’s customized onsite technical, scientific, or business writing workshops, or online courses, call us, visit our website, or email us.